MANUFACTURING CAPABILITIES
Punching and Stamping Services
Punching and Stamping Services
Punching is a process that uses a CNC machine to shear, notch, and punch angles and flat bars. Porous Metal Filters utilizes state-of-the-art equipment to plasma cut, punch, drill, and tap metal components to produce items in a cost effective manner.
Punching holes with a punch press is one of the most mature technologies in metal fabrication, and yet it’s still one of the most misunderstood. Modern machines and tooling have turned the punch press into the Swiss army knife of the fab shop. It punches holes, just a few here and there or in a dense perforation. It cuts large panels. It forms louvers, embosses, and other complex shapes, and in some cases bends flanges several inches high.
Still, because the punch press can do so much, processing variables abound, and if they’re not accounted for, part quality and throughput can suffer. Understanding a few punching fundamentals can go a long way in ensuring that the multitude of processing variables remain well under control.
Our sheet and plate machines have computer numerical controls (CNC) that allow for production repeatability and are programmed from CAD software to reduce errors. Typical material thicknesses for punching is ½” thick and below.
Porous Metal Filters offers CNC metal forming and bending services to produce components and fabricated parts for subassemblies. From simple 90° bends to complex sequences with multiple bends, our press brakes can form small and large parts.
Technology, skill, and process controls allow formability and repeatability to meet customer demand. PMF can handle a wide range of material grades, thickness, and sizes.
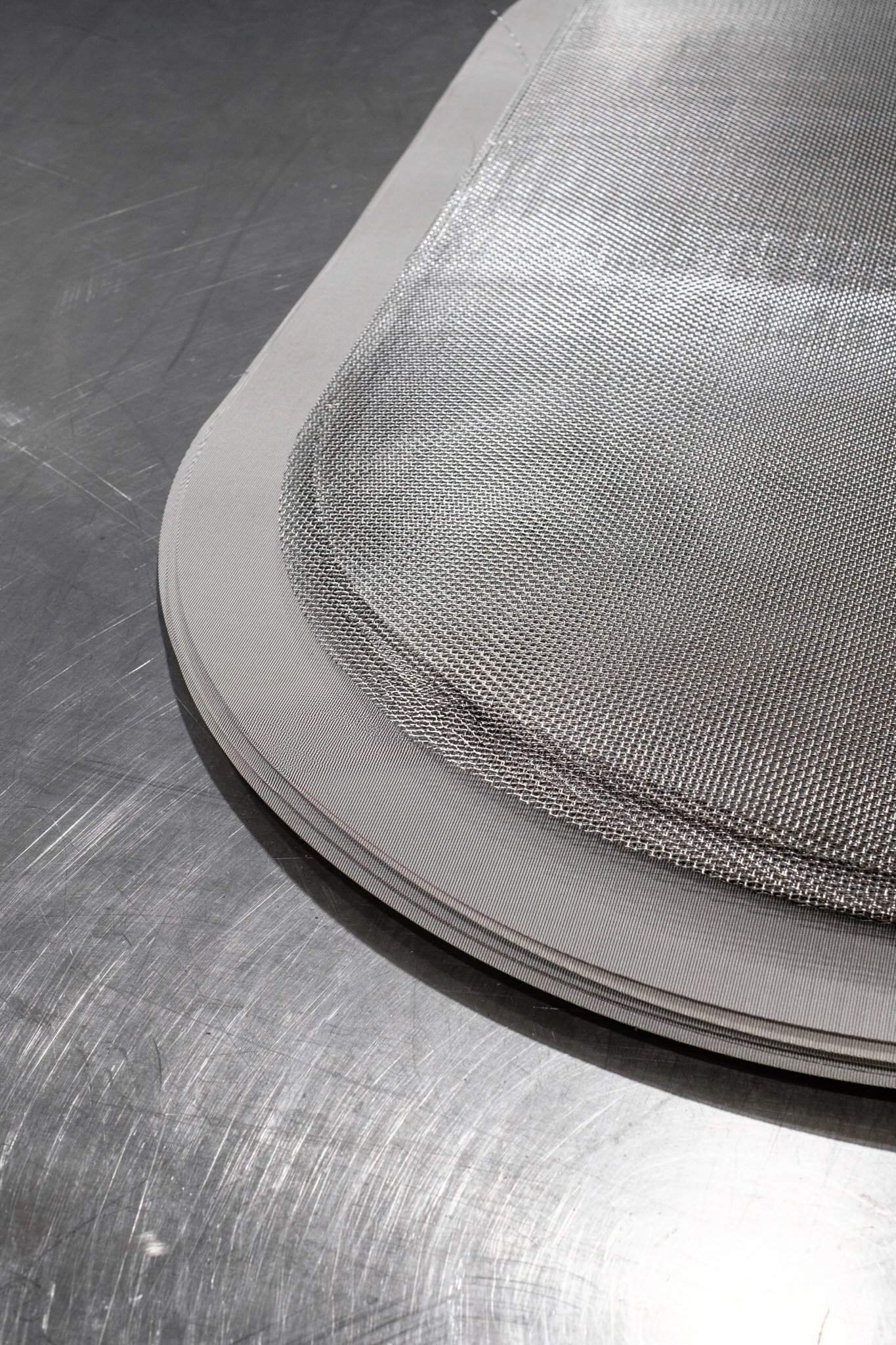
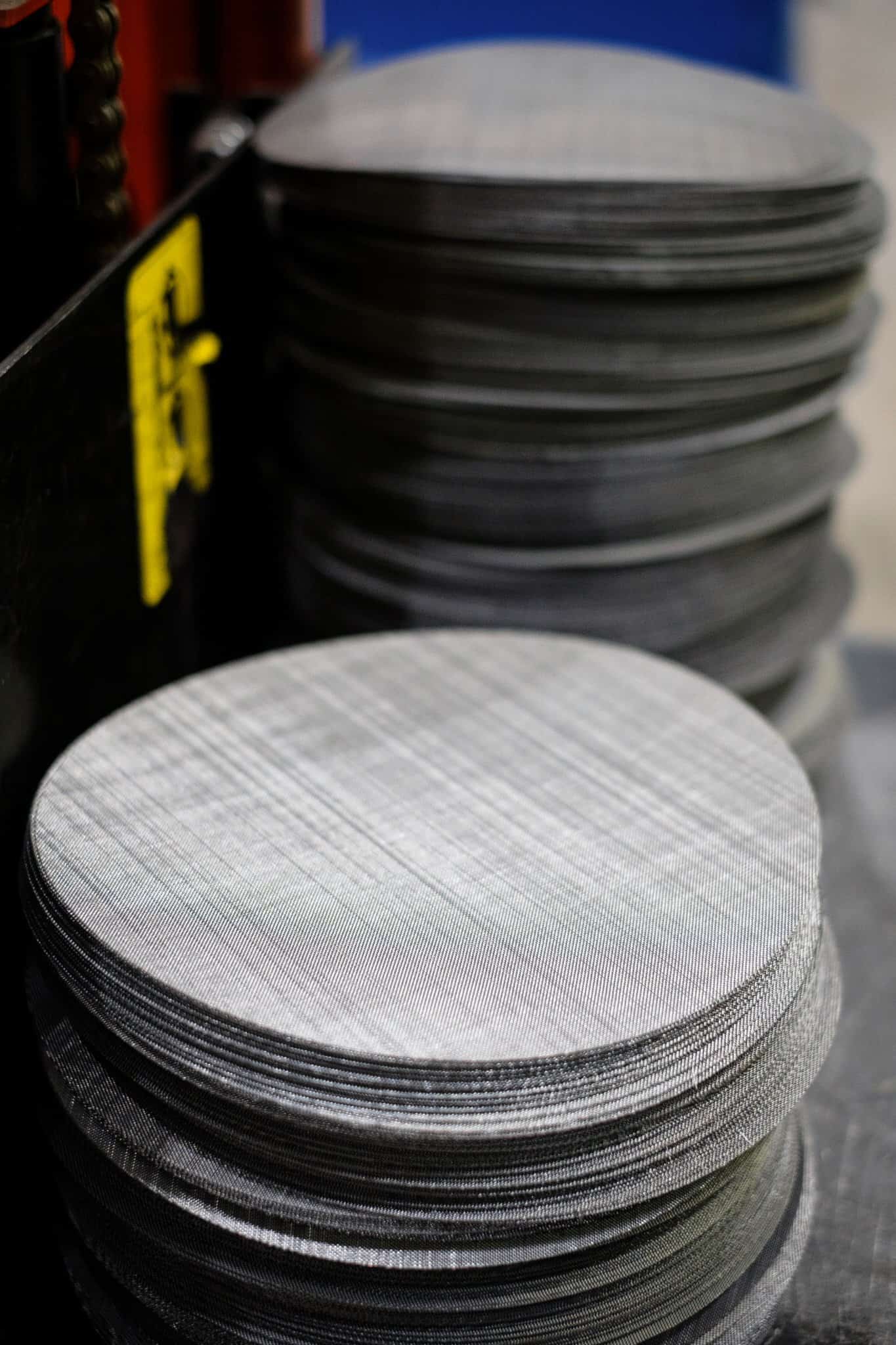
Shaping & Punching Wire Mesh
DWT utilizes shaping and punching to provide custom shapes to meet clients’ specifications and requirements. We offer economical stamped parts in many configurations as well as laser cut or plasma cut parts for prototypes and small run parts. For stampings, we have a wide range of standard round dies. If you are unsure of your needs, or want additional information on our cutting or stamping capabilities, please contact us to learn more.
Custom Tooling
Custom tooling is available made to order. PMF has in house tooling capabilities helping to save time and cost. We also offer laser cutting for rapid prototyping.
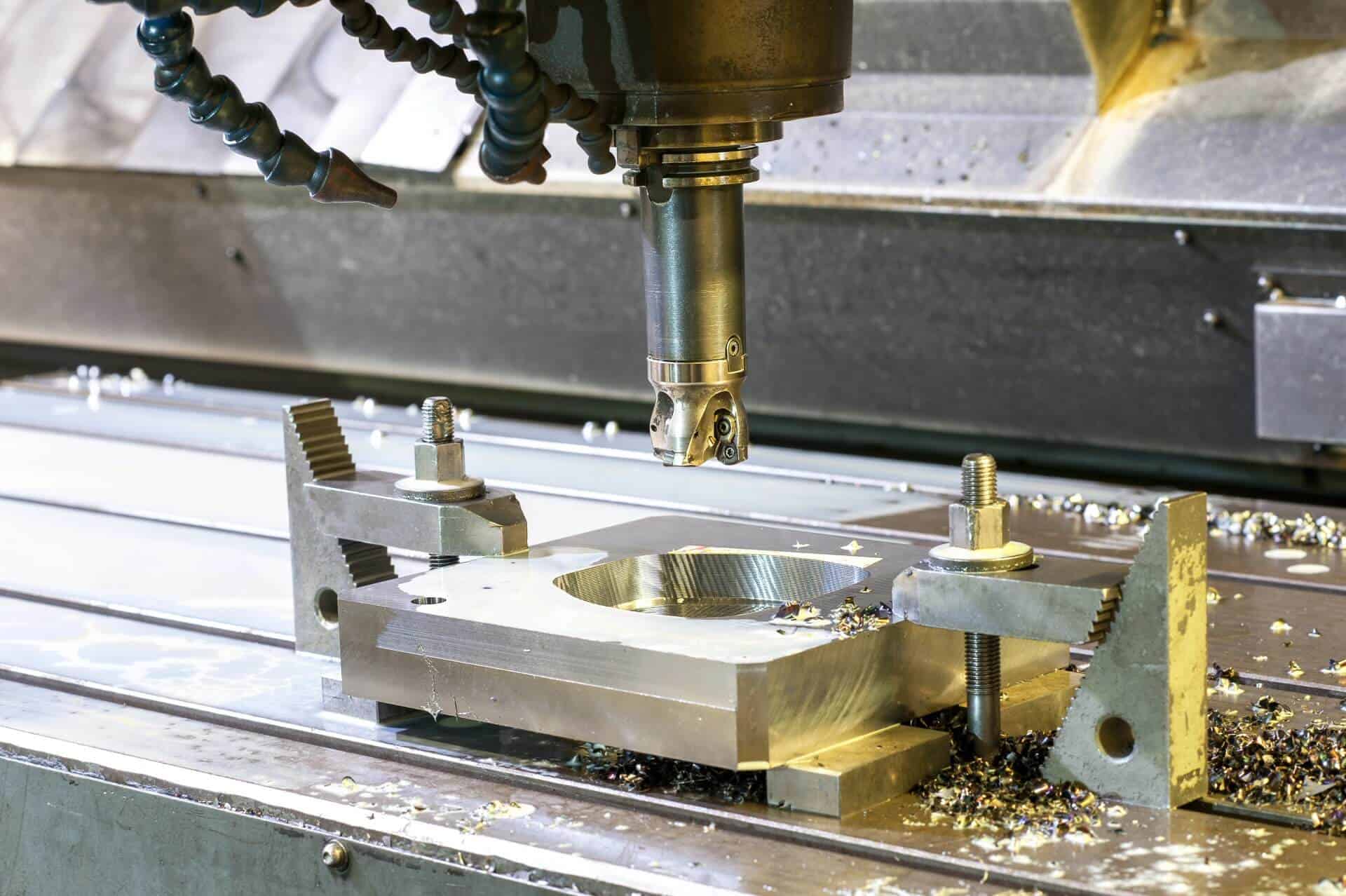
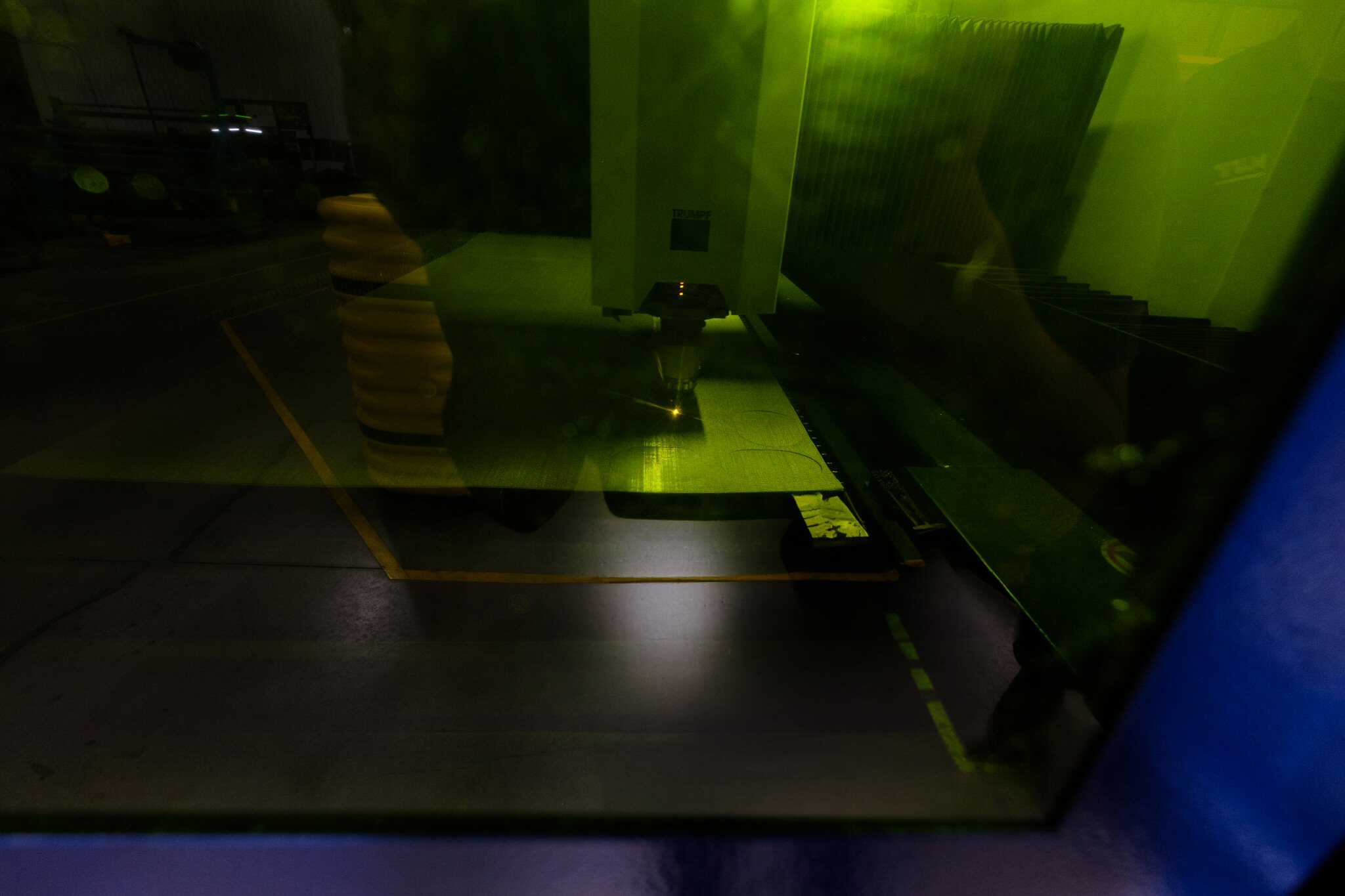
Porous Metal Filters is ISO 9001 Certified, and all our products are manufactured to the highest quality standards. Our staff is available to help you design the wire filtration product that will meet your design requirements and budget. Contact us today for more information about our products.
Your One-Stop Solution for Advanced Filtration and Metal Fabrication
We invite you to explore and discover how PMF can transform your filtration and separation challenges into opportunities for growth and success. Join us on this exciting journey as we reshape industries, one innovative filter at a time. Together, let's unlock the true potential of porous metal filtration. Give us a call, stop by for a free tour of the facility, or fill out our contact form and we'll gladly assist you.
Find Exactly What You Need
COMPANY
INDUSTRIES & APPLICATIONS
Automotive
Bulk & Powder Handling
Chemical Processing
Chromatography
Crude Oil Processing
Filtration Industry
Fuel Cells & Re-Formers
Gasification
Hot Gas Filtration
Industrial Filtration
Industrial Water Management
Irrigation Filtration
Liquid Filtration
Noise Abatement
Oil & Gas
Pharmaceutical
Plant Oil Extraction
Power Generation
Renewable Energy
Aerospace Filters
Ballast Water Filters
Chemical & Industrial Spargers
Chromatography Frits
Demineralizer Filters
Flame/Spark Arrestors
Flood Filters
Fluidizing Media
Gasification Filters
Hot Gas Filters
Irrigation Filters
Metallic Filter Cartridges
Metallic Memberane Support for Hydrogen
Nutsche Filters
Porous Metal Plate
Sand Screens
Sintered Metal Fiber
Sintered Wire Cloth
Temporary Strainers & Baskets
CAPABILITIES
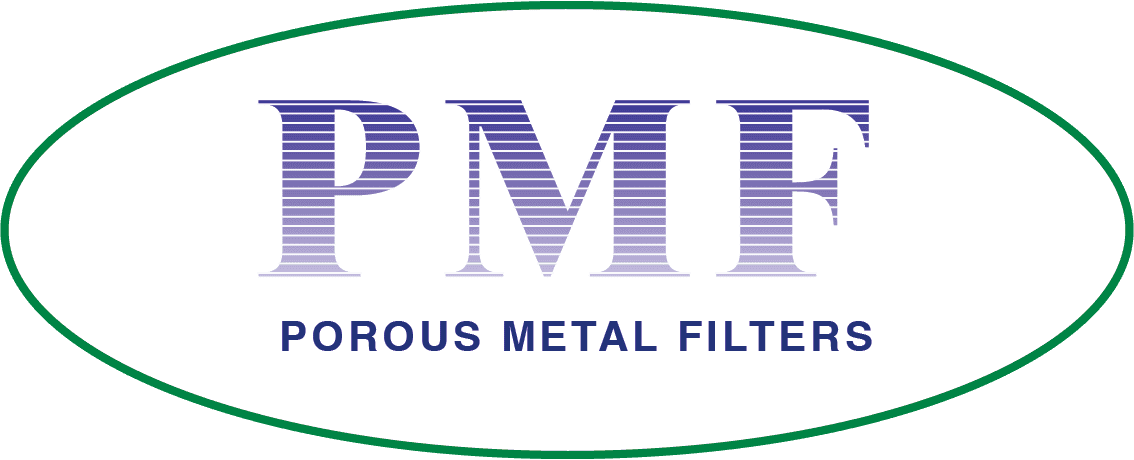
Porous Metal Filters provides solutions for industrial filtration, separation, flow control, noise reduction, powder fluidization, and other applications through our SINTERPORE® brand of diffusion bonded (sintered) porous metal materials. Porous Metal Filters’ goal is to utilize its extensive experience to promote porous metal filters for the next generation of advanced filtration and separation products.
Physical Address
19994 Hickory Twig Way
Spring, TX 77388 USA
Mailing Address
P.O. Box 3019
Spring, TX 77383
PHONE
(833) 707-9222 toll free
(281) 719-1352 local
(281) 719-1351 fax